FAQ (Frequently Asked Questions)
We’re here to help and answer any questions you may have. To help in that effort, we have included some common questions, and the answers, about Spin-On Glass below.
Spin-on Glass FAQs
Do spin-on dopants give uniform doping?
A. Spin-on doping is much more uniform than gas diffusion doping in a furnace tube. Typically, variance across a wafer is between 0.5% and 1% and variance wafer to wafer ranges between 1% to 2%.
Do phosphorous spin-on dopants have difficult trade restrictions?
A. All spin-on dopants must be shipped with normal care. Phosphorous does not have the same restrictions as POCl shipments, which can be very difficult to ship.
How do spin-on dopants improve throughput for antimony doping?
A. Solid source doping with antimony trioxide uses slots for the doping source.This decreases throughput and uniformity. It can also increase maintenance costs for furnace tubes. Usually 3 furnace tubes are required (1 for predep, 1 for drive in & 1 for source slice storage)
Is auto-doping a problem with spin-on dopants?
A. With spin-on dopants, the doping material is confined to a large degree in a silicate matrix. The dopant is less likely to diffuse into the backsides of the wafer from tube contamination or from the front side.
What are typical junction depths for common dopants?
A. Please see table below:
Element | Typical Junction Depth |
Antimony | 2 to 8um |
Phosphorous | 0.5 to 8 um |
Arsenic | 1.5-8um |
Boron | Base 0.2 to 0.8 um Isolation 3 to 11 |
Gallium | um Gallium junction depth can be considerably deeper. |
Does maintenance on my furnace tubes change when I use SOD?
A. Maintenance decreases with SOD use compared to gas or solid sources.
What is the shelf life of your product?
Spin-on Glass | Room Temperature | 2-4°C |
P-220 | 9 months | >12 months |
P-230 | 6 months | >12 months |
P-640 | 3 months | >12 months |
P-260 | 4 months | >12 months |
P-280 | 2 months | >12 months |
B-1000 | 6 months | >12 months |
B-1200 | 3 months | >12 months |
B-1500 | 2 months | >12 months |
NDG-2000 | 3 months | >12 months |
NDG-5000 | 3 months | >12 months |
NDG-7000 | 3 months | >12 months |
Ga-100 | 2 months | >12 months |
Ag-135 | 2 months | >12 months |
Cu-345 | 3 months | >12 months |
Li-260 | 3 months | >12 months |
Ti-140 | 3 months | >12 months |
Ti-452 | 3 months | >12 months |
Al-250 | 3 months | >12 months |
Au-500 | 3 months | >12 months |
Pt-401 | 3 months | >12 months |
Yt-228 | 3 months | >12 months |
Ba-234 | 3 months | >12 months |
YtBaCu-123 | 3 months | >12 months |
Sn-365 | 3 months | >12 months |
Sb-380 | 3 months | >12 months |
P-640 | 3 months | >12 months |
Zn-640 | 2 months | >12 months |
ZnP-640 | 2 months | >12 months |
ZnAs-650 | 2 months | >12 months |
GaAl-330 | 3 months | >12 months |
Nd-350 | 3 months | >12 months |
BPSG-839 | 3 months | >12 months |
BPSG-50 | 3 months | >12 months |
In-345 | 3 months | >12 months |
What is the shrinkage on final cure?
A. For spin-on glass materials, shrinkage on a final cure is 12-15% depending upon dopant type and concentration.
What is the intrinsic film stress of your material?
A. 200 mega Pascal for silicates.
Does your Spin-On Glass formulations contain water?
A. Several of our materials use the sol-gel reaction and require water at a 5% to 10% level.
What is the refractive index of your spin-on glass materials?
A. Our low density material has an RI of 1.45, our fully densified material has a RI of 1.44, and we can manufacture custom materials with indexes of 1.42 to 2.5.
What is the concentration of the dopant in your film?
A. Higher product numbers indicate higher dopant concentration. For example P-220 is our lowest phosphorous doped SOG and P-280 is the highest. Concentrations range from a fraction to several weight % in the glass.
What is a typical application method for your Spin-On Glass and spin-on dopant materials?
A. A typical application method is: utilizing a photoresist type spinner, load and center the wafer onto vacuum chuck, dispense SOG covering 80% of the wafer, spin at 3500 RPM for 30 seconds, bake at 200C for 5 minutes. Load into quartz boat, slow push into furnace (or ramp from lower temp., see application guide for specific dopants) diffuse in recommended ambient (usually 2% O2 in N2) for time & temp to achieve desired Xj and sheet resistance, slow pull or ramp down the furnace, strip glass in BOE (when using etchants containing HF, use extreme caution! HF is a dangerous material!). Measure sheet resistance and junction depth.
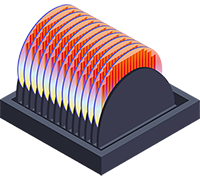
Spin-On Glass Products
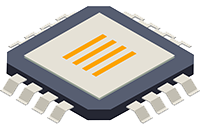